Finding the Sweet Spot in Plastic Cutting Tools
Finding the Sweet Spot in Plastic Cutting Tools
There are a number of factors to consider when setting up to machine plastics. Most importantly, plastic has a higher thermal expansion rate than most other materials, such as metal or wood products. Thermal expansion is the tendency of the material to change volume in response to the heat introduced during the formation of chips created during the cutting process. Reducing thermal expansion is key to producing clean and effective cutting in any plastic cutting operation.
Following are some key tips to reducing thermal expansion and improving your cutting success. The first thing to consider is tool geometry and quality. This is true for any type of cutting tool: Router bits, saw blades and wing-type cutters. For this article we will be discussing router bits, but the techniques discussed are applicable across the board.
Plastics fall into two main categories: Hard and Soft. Harder plastics, or those with a higher durometer rating, generally have a lower rate of thermal expansion. Softer plastics will obviously have the opposite properties. Softer plastics tend to be more difficult to cut due to the fact that it will tend to “push” out of the way of the cutting edge of the tool, increasing friction and thus heat, introduced to the chip formation. When the threshold of heat exceeds the melting point of the material the chips being formed, the chips will melt causing a problem.
Generally we select tooling with higher shear or helix angle when cutting softer plastics. The higher shear angle can reduce cutting pressure, thus reduce heat created. However, factors such as material thickness and hold down will limit the ability to introduce high shear tools into the cut.
One thing we have recently introduced to our line of plastics bits is a highly polished flute. High polish dramatically reduces friction created during the cut. This will create cleaner cuts in most applications.
Selecting the proper chip load is another important factor for proper cutting. Hitting the “Sweet Spot” is one of the most critical factors for successfully cutting. The window for the proper chip load is much smaller for plastics than in any other material. Typically, one or two thousandths of an inch will make the difference for plastics where wood, for example, can machine well across tens of thousandths of an inch. Chips load is calculated using the following formula:
Chip Load = Feed Rate (IPM)/(# Cutting Teeth X RPM)
Chip loads for plastics are generally between .004” to .008”. The important point is that plastics will have a very small “window” of acceptable chip load and all conditions of the cut will factor into what chip load will be successful in a particular application. Learn to calculate chip loads in your application and make small incremental adjustments to “Dial in” what works best for your particular application.
Tool deflection is another factor that needs to be addressed in order to reduce friction created at the cutting site. Router tooling, cutting tool diameter, geometry and tool holding all play a role. In general, larger tool diameter will deflect less, thus reducing tool deflection. Work with your supplier to select the best tool geometry/diameter that will work for your application. The tool itself is driven by the tool holding device. There are numerous options for driving your cutting tool. The important point is to realize that the more substantial your tool holding is, the better the results you will see in cutting.
The final area to consider to improve your cut quality is “Part Hold Down”. Again, the more rigidly the part is held, the better your results will be. When fixturing parts, it is imperative that the part be held securely as close to the cutting site as possible. This is especially true for thinner materials. If the part can fluctuate due to part instability, it can make the difference between a good cut quality and a poor one. In a vacuum hold down situation you want your gasket seal as close to the cut edge as possible. If you are clamping parts, the same is true. Basically, the more you invest in fixturing, the better your results will be.
In closing, to increase your cut quality in plastics there are four things to concentrate on. First: select the proper tool with the optimal tool geometry for your application. Second: make sure that your tool is run at the optimal parameters for your application (feed rate). Third: Review your tool holding devices and make sure to optimize as best you can. And finally, make sure your parts are held in the best way possible.
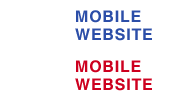
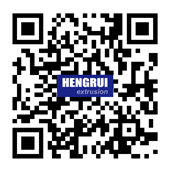