What is Single Screw Extrusion Machinery?
There are numerous hardware considerations that can influence the quality of an extrusion. For example,screw geometry, screw rotation speed, and barrel heater temperature must be calibrated to suit the specific type of plastic being fabricated. Incompatible settings may hinder production or even damage the equipment.
As the main component of an extruder, the screw handles several tasks, including moving, melting, and pumping the plastic before it sends it through the die. A motor-driven gearbox with variable speeds usually turns the screw, which is enclosed in a tight fitting barrel. The mechanism is divided into three sections tailored to perform a sequence of specific tasks.
The feed section, located at the rear of the screw apparatus, contains a hopper that delivers resin pellets into the machine. As the screw turns, it draws the plastic forward with threads, or “flights.” Barrel heaters help the plastic develop a tacky skin to improve friction between the plastic and the barrel wall. Without this friction, it would be difficult for the plastic to achieve lateral movement.
As the plastic moves forward, it enters the transition, or melt, section. In this stage, the root diameter of the screw increases, while the flights decrease in size in order to melt the plastic by compressing and shearing it against the barrel wall.
The barrier screw is specifically designed with the transition section in mind. These screws have special barrier flights that improve mixing and melting by dividing the molten and solid plastic into separate channels. The barrier flights are smaller in diameter than regular flights, and provide a passage for melted plastic while blocking the solid pellets until they liquefy. As the plastic continues along the transition section, the melt channel increases in width, while the solid section decreases until there are no plastic pellets left.
After the plastic is melted and compressed, it is channeled into the metering section. Here, the plastic undergoes pressurized pumping, while the root diameter of the screw and the flight size remain constant. Some extrusion screws use special mixing heads to homogenize the plastic before it travels into the next section.
As the main component of an extruder, the screw handles several tasks, including moving, melting, and pumping the plastic before it sends it through the die. A motor-driven gearbox with variable speeds usually turns the screw, which is enclosed in a tight fitting barrel. The mechanism is divided into three sections tailored to perform a sequence of specific tasks.
The feed section, located at the rear of the screw apparatus, contains a hopper that delivers resin pellets into the machine. As the screw turns, it draws the plastic forward with threads, or “flights.” Barrel heaters help the plastic develop a tacky skin to improve friction between the plastic and the barrel wall. Without this friction, it would be difficult for the plastic to achieve lateral movement.
As the plastic moves forward, it enters the transition, or melt, section. In this stage, the root diameter of the screw increases, while the flights decrease in size in order to melt the plastic by compressing and shearing it against the barrel wall.
The barrier screw is specifically designed with the transition section in mind. These screws have special barrier flights that improve mixing and melting by dividing the molten and solid plastic into separate channels. The barrier flights are smaller in diameter than regular flights, and provide a passage for melted plastic while blocking the solid pellets until they liquefy. As the plastic continues along the transition section, the melt channel increases in width, while the solid section decreases until there are no plastic pellets left.
After the plastic is melted and compressed, it is channeled into the metering section. Here, the plastic undergoes pressurized pumping, while the root diameter of the screw and the flight size remain constant. Some extrusion screws use special mixing heads to homogenize the plastic before it travels into the next section.
Subscribe now
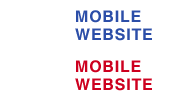
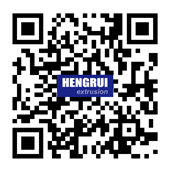